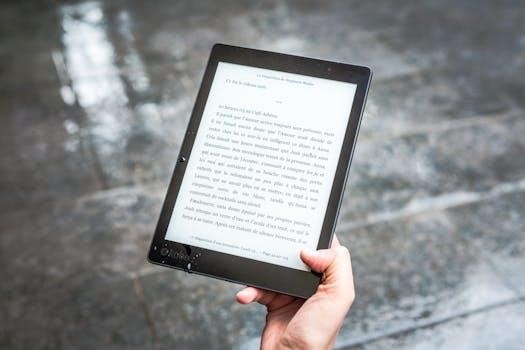
Lubrication failure occurs when goals are not achieved, such as minimizing friction, wear, and heat. It compromises machine reliability and lifespan; Failures can arise from various causes related to lubricant properties and use. Identifying these issues is crucial for preventive maintenance.
Defining Lubricant Failure
Lubricant failure is fundamentally a breakdown in achieving the intended goals of lubrication. This includes maintaining a film to separate moving parts, minimizing friction and wear, and preventing excessive heat. It also entails acting as a heat transfer fluid, transferring force in hydraulic systems, and removing contaminants effectively. A lubricant should also prevent sludge and varnish buildup, remain in place despite clearances, simplify maintenance, and protect against corrosion. When one or more of these objectives are not met, it constitutes a lubrication failure, which can manifest through various failure modes stemming from diverse causes. Essentially, a lubrication failure is any situation where the lubricant’s performance is insufficient, jeopardizing machine reliability or longevity.
Major Areas of Lubricant Failure Modes
Lubricant failure modes commonly occur due to temperature issues, moisture, foreign particles, viscosity problems, and contamination. Understanding these areas is crucial for preventing lubrication failures and ensuring machinery reliability.
Temperature-Related Failures
Elevated temperatures significantly impact lubricant performance, causing thinning and reduced effectiveness. High heat accelerates oxidation, forming harmful byproducts like aldehydes and carboxylic acids. These reactions degrade the lubricant, diminishing its protective qualities. Overfilling lubrication systems can also contribute to temperature failures, creating hot running conditions. Moreover, rapid temperature degradation and oxidation were common in early lubricants, leading to short lifespans. By identifying and eliminating the root causes of excessive heat, lubricant life can be extended. Factors like incorrect application, overloads, or inadequate cooling should be addressed. These issues can trigger chain reactions and wear particles, perpetuating failure modes.
Moisture-Induced Failures
Moisture contamination is a significant contributor to lubricant failure, often leading to accelerated degradation and reduced component lifespan. Even small amounts of water can initiate corrosion and rust, damaging critical machine parts. Water can also cause additive depletion, affecting the lubricant’s ability to protect surfaces. The presence of moisture promotes the formation of sludge and varnish, which can clog lubrication systems and impede oil flow. Furthermore, moisture can interfere with the lubricant’s ability to maintain a proper film thickness, increasing friction and wear. Addressing this failure mode includes implementing proper sealing and filtration systems.
Failures Due to Foreign Materials and Particles
Foreign materials and particle contamination are major causes of lubricant failure, introducing abrasive elements into the system. These particles, often dirt or wear debris, disrupt the lubricant film, causing increased friction and wear on machine components. Even particles as small as 5 to 10 microns, can compromise the lubricant film, leading to accelerated wear. These contaminants can also act as catalysts for oxidation, further degrading the lubricant. The accumulation of particles can clog filters and restrict oil flow, leading to inadequate lubrication. Proper filtration and sealing are crucial to prevent particle contamination and ensure reliable machine operation.
Viscosity-Related Lubricant Failures
Viscosity is a critical property of a lubricant, and deviations from the recommended range can lead to significant failures. If the viscosity is too low, the lubricant film may not be sufficient to separate moving parts, resulting in increased friction, wear, and heat generation. High temperatures cause oil thinning, further reducing its effectiveness. Conversely, if the viscosity is too high, the lubricant may not flow properly, leading to inadequate lubrication and increased energy consumption. Incorrect lubricant selection, not matching the machine’s requirements, is a primary cause of viscosity-related failures. It’s crucial to choose a lubricant that maintains its viscosity under operating conditions.
Failures Caused by Contamination
Contamination is a major contributor to lubricant failure, with particles, moisture, and chemical substances causing significant issues. Foreign materials like dirt, dust, and wear particles can disrupt the lubricant film, leading to abrasion, erosion, and fatigue failures. Moisture contamination can cause rust and corrosion, further degrading the lubricant’s performance and the machine’s components. Chemical contaminants, such as glycol or stored chemicals, can react with the lubricant, causing oxidation and sludge formation. Contamination can lead to reduced lubricant effectiveness, premature wear, and ultimately, machine failure. Controlling and preventing contamination through filtration and proper handling is crucial for maintaining lubricant and machine health.
Root Causes of Lubrication Failure
Lubricant failure stems from issues with lubricant properties, lubrication systems, handling practices, machine operation, and contamination. These factors contribute to breakdowns and reduced machine lifespan if unaddressed.
Inadequate Lubricant Properties and Performance
The lubricant’s base oil and additives work in tandem to achieve specific characteristics. Inadequate properties such as incorrect viscosity, rapid temperature degradation, and oxidation contribute to lubricant failure. If the lubricant cannot maintain a sufficient film, it leads to increased friction and wear. Furthermore, the formation of gums, varnish, and sludge due to oxidation reactions further impairs performance. The lubricant’s inability to properly cool components or transfer force also indicates a property-related failure. Selecting a lubricant not suited for the application is a common cause that accelerates failure.
Lubrication System Issues
Failures within the lubrication system itself can significantly contribute to overall lubricant failure. These issues include low oil levels, which can lead to lubricant starvation and increased wear. Additionally, problems with the system’s ability to effectively filter or remove contaminants will accelerate degradation and reduce the lubricant’s effectiveness. Inadequate flow rates, improper distribution, or blockages within the system can also prevent the lubricant from reaching critical components. Moreover, if the system is not designed to maintain proper temperature control, it can negatively affect the lubricant’s viscosity, further adding to the problem.
Improper Lubricant Handling and Application Practices
Incorrect handling and application of lubricants are major contributors to premature failures. This includes using the wrong type or grade of lubricant, which can lead to inadequate protection and increased wear. Over or under-lubricating components can also be detrimental, causing temperature issues or lubricant starvation. Furthermore, storing lubricants improperly exposes them to contaminants and moisture, accelerating degradation. Lack of proper procedures during application, such as using contaminated equipment or introducing dirt, will also compromise the lubricant’s performance. The failure to follow recommended relubrication schedules exacerbates the problem, leading to insufficient lubrication.
Machine Operation Factors Contributing to Failure
Machine operation significantly impacts lubricant performance and lifespan. Operating machinery beyond its designed capacity or at excessive speeds generates higher temperatures, which degrades lubricants and reduces their effectiveness. Inadequate warm-up periods can also lead to lubrication issues, as lubricants may not reach the optimal operating temperature. Moreover, frequent starts and stops can create boundary lubrication conditions, increasing wear. Overloading the machine puts excessive stress on lubricated parts. Vibration and misalignment contribute to lubricant film breakdown, leading to increased friction and premature failure. All these factors contribute to lubricant degradation and ultimately, machine failure.
Consequences of Lubricant Failure
Lubricant failure leads to machine breakdowns, costly downtime, and reduced equipment lifespan. Inadequate lubrication increases friction and wear, causing premature component failure and necessitating expensive repairs or replacements.
Machine Failure and Downtime
Lubricant failure is a significant contributor to machine breakdowns, resulting in costly downtime. When lubrication fails, moving parts experience increased friction and wear, leading to component damage and eventually, machine failure. This can manifest in various ways, from minor performance issues to catastrophic breakdowns. Such failures disrupt production schedules, causing lost output and financial losses. Identifying and addressing the root causes of lubrication failure is critical to prevent such disruptions and maintain operational efficiency. The downtime resulting from machine failures not only impacts productivity but also incurs expenses related to repairs and replacements, further highlighting the importance of proper lubrication practices.
Reduced Equipment Lifespan
Lubricant failure significantly contributes to the premature aging and reduced lifespan of machinery. When lubrication is inadequate, parts experience increased friction, leading to accelerated wear and tear. This degradation of components weakens the equipment’s structure, making it more susceptible to failure. Furthermore, the buildup of contaminants and byproducts due to lubricant degradation can corrode and damage internal mechanisms, shortening the useful life of machines. This can lead to costly replacements and frequent repairs. Proper lubrication is essential for maximizing the durability and longevity of equipment, minimizing the need for premature replacement, and ensuring efficient operations.
Preventive Measures and Proactive Strategies
Implementing proper lubrication practices and condition monitoring are crucial for preventing failures. Early detection of issues allows for timely intervention, extending equipment life and ensuring reliable operation.
Importance of Proper Lubrication Practices
Proper lubrication practices are essential for maintaining machinery health and preventing failures. These practices encompass various aspects, including the correct selection of lubricants based on the application, and ensuring that the lubricant is applied in the right amount and frequency. Furthermore, it is crucial to avoid overfilling or underfilling lubrication points, as both can lead to temperature-related issues. Proper lubrication methods also include the implementation of effective sealing and filtration systems to prevent contaminants from entering the lubrication system. Training personnel on lubrication excellence practices is key to minimizing failures caused by improper handling and application. These practices also help to avoid wear, heat generation, and other issues.
Condition Monitoring and Early Detection
Condition monitoring is crucial for the early detection of potential lubrication failures, allowing for proactive maintenance. This involves regularly assessing the lubricant’s condition through methods like oil analysis, which can detect oxidation, contamination, and viscosity changes. Furthermore, monitoring machine performance indicators such as temperature, vibration, and noise levels can reveal lubrication problems before they escalate into major failures. Implementing a robust condition monitoring program enables maintenance personnel to identify and address issues promptly, minimizing downtime and repair costs. This also includes regularly checking lubricant levels and inspecting for leaks. Early detection will help prevent catastrophic failures and extend the lifespan of the equipment.